Abdon Food AB let us share their story in five episodes. We are going to follow their digital transformation and the experiences they have had, and will have, implementing the Connectitude IIoT Platform™. IIoT means the Industrial Internet of Things, and is an integral part of Industry 4.0.
Episode release plan
- In the beginning. Strategies and coincidences that led to a partnership in IIoT.
- The Pilot. The first Proof of Concept project at the Björnekulla production site.
- Scaling up. The continuous rollout, from a technical view, and from the staff’s perspective.
- The impact. Six months later – how is IIoT part of the daily routines at a production site.
- The bottom lines. What results of the IIoT investment can the CEO and CFO see in their numbers?
Episode 1. In the Beginning
Some facts
Abdon Food AB might not be as widely known as their household brands Finax and Björnekulla. Finax is as synonymous to cereal, bread, flour and oats as Björnekulla is for jam and pickles to most Swedes. Ramlösa Kvarn produce special purpose flours for the growing high-end market. With numerous mills, bakeries and production sites in the very south of Scandinavia, the annual turnover is around $100M and the number of employees is approximately 300.
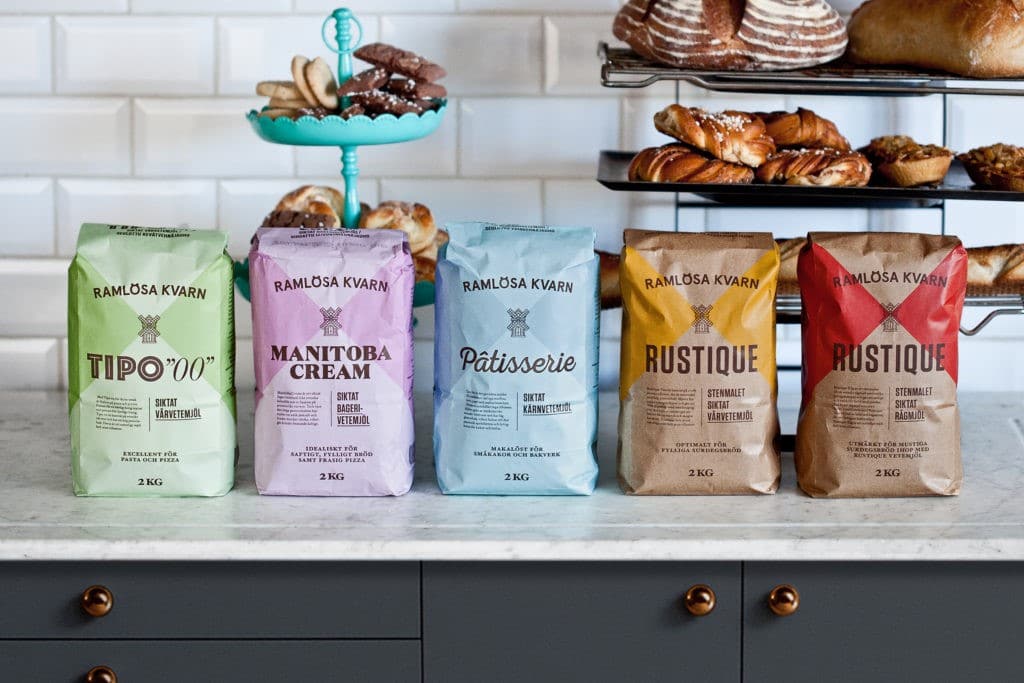
Early to adopt, keen to adapt
It is in Abdon Food’s DNA to be forerunners. The founding brothers, Leif and Rolf Abdon, constructed the world’s first fully automatic grain mill for their production of flour and oats. They brought muesli to Scandinavia in the 70’s, and they have been pioneers in gluten free products since the early 80’s. For them it is natural that their strategic plan for IT and systems for production control is focused on solutions that easily can adapt to changes in technology, production processes and in their business domains.
Commitments and Commandments
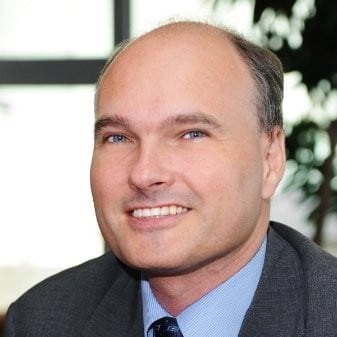
Michael Jörgensen is CTO at Abdon Food AB since 2018. With a vast experience as CTO in fintech and telecom, he brought agile software development methods to speed up the digital transformation. Projects in processing and manufacturing industries, are often characterized by long-term investments, preceded by extensive feasibility studies. “It is more important to establish a sustainable philosophy for architecture and infrastructure than to have all the feature designs and details in place when you start a project. I have seen too many large and overly planned IT projects being obsolete or running out of funding before they are released. Iterative development is not only more flexible over a timeline, it limits the economic risk when you can create and test new features in many short sprints.
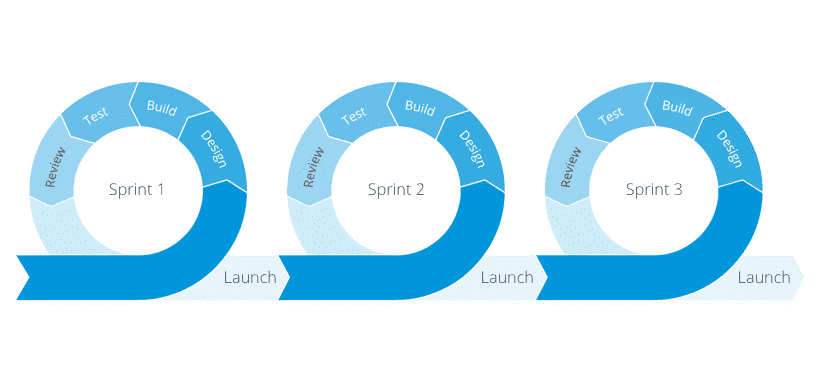
The outlines for the digital roadmap was set two years ago when Abdon Food AB selected and implemented a new ERP system. It had to be a cloud solution providing SaaS (Software as a Service). “We have designed a common data warehouse where we can create reports with information from several different data sources such as our SCADA system, the business system and our IIoT solution. At each production facility, there are some Microsoft Excel mavericks, who can create their own reports. For more formal reports that are to be read frequently and by many, we usually design them in Microsoft Power BI. New systems are easily added as long as they have public APIs allowing a seamless integration.
Sweeping the market
“We are constantly monitoring what is happening in the market in system solutions for production and Industry 4.0. Software in the industrial automation market is usually closely linked to manufacturers of HMIs, PLCs and sensors. This creates dependencies and causes a more rigid infrastructure. Alternatively the staff needs different systems for different types of machines, which is highly impractical and expensive.
One of our production managers has the need to quickly see the overall effects when he changes settings for the machines and production lines. He wants to be able to add new measurement values in histograms and adjust alarm levels and such more easily, without having to change the SCADA and the PLC configuration.
We started by researching some well-known systems for monitoring the OEE, Overall Equipment Effectiveness. Most of them had very extensive functionality. Unfortunately, both license and implementation costs were too high, and too complex, in relation to what we primarily wanted to solve. During the same period, we also looked for a SaaS solution for SCADA and production control. What was presented was mainly traditional softwares, hosted on external servers with access via VPN. For us, that offers no benefits whatsoever.”
One stone, three birds
“About six months ago, a colleague of mine saw an advertisment about a cloud platform for IIoT. It had much of what we wanted regarding features and architecture. What appealed to us was the compatibility with various brands of hardware, and the use of well-known technologies for the software, with a backend in .NET and web-based frontend. Also, the platform’s local edge, on location in the production facilities, can be fully operational even when the Internet connection is lost. We contacted them and after a meeting we saw that their take on having basic functions within OEE and SCADA would suffice. Our curiosity about using sensors and machines connected via LoRa also matched the supplier’s ambitions. We could now possibly solve three needs with one solution. And that was just for starters.
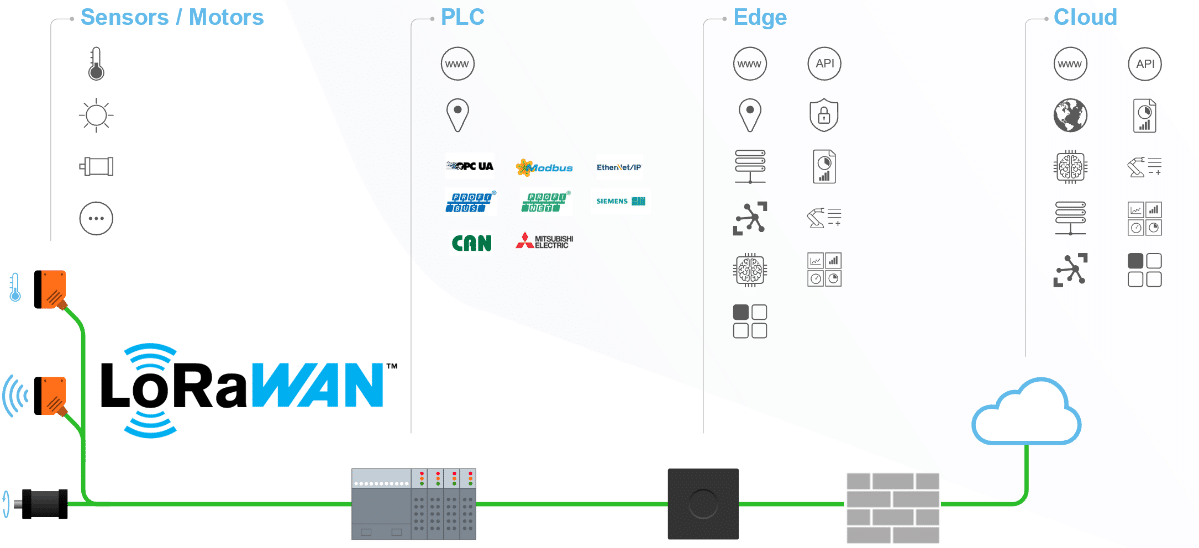
Extended development teams
“We try to keep our IT department as lean as possible. We take pride in deliver great solutions, but not necessarily by developing all components ourselves. This IIoT platform had most of the basic features we needed. Features we wanted to develop or customize, could easily be divided into sprints of our preferred size. We agreed with the supplier for a joint venture on an OEE solution, designed for our needs. The consensus in the ideas for its design and how to conduct the PoC (Proof of Concept) made us feel safe. We want collaboration partners who not only deliver what we specify, but who also can come up with ideas and dare to say if they see a better solution to something. Moreover, the estimated price for the entire PoC was actually lower than the feasibility study for some of the larger OEE systems we were looking at, so we said “GO!” in November 2019.”
Seeing is believing
”What we initially bought was a promising vision, to be built on a platform we just had seen in controlled and staged demos. Of course, I felt some level of uncertainty myself, before we were up and running. Especially when the colleagues outside the project could not get the full feel and touch of the final solution. When the IIoT platform was connected to a selection of production lines, it instantly became easier to explain and visualize concepts for the upcoming features we consider adding. The need for more sensors on a machine or in the buildings also got more obvious. The faster you can finish your first PoC, the faster you will get all the stakeholders and the staff onboard. Hence, my recommendation is to keep it neat and focused on a few but tangible effects.”
Any bumps in the road?
In the next episode of IIoT in reality – The Finax experience we will go deeper and more technical into the first PoC. Björnekulla is a brand within Abdon Food AB specializing on producing fruit jams and pickled vegetables. The production manager at Abdon Food AB, Mathias Stendahl, chose the Björnekulla site in Svalöv for the PoC. He also defined the goals and success criterias for the first version of the OEE module. His mission is to be able to tweak parameters in the production and get feedback on the effects as quickly as possible. Stay tuned!