Abdon Food AB let us share their story in five episodes. We are going to follow their digital transformation and the experiences they have had and will have, implementing the Connectitude IIoT Platform™. IIoT means the Industrial Internet of Things and is an integral part of Industry 4.0. Episode 2: The pilot, tells the inside story of the first pilot project at Björnekulla.
Episode release plan
- In the beginning. Strategies and coincidences that led to a partnership in IIoT.
- The Pilot. The first Proof of Concept project at the Björnekulla production site.
- Scaling up. The continuous rollout, from a technical view, and the staff’s perspective.
- The impact. Six months later – how is IIoT part of the daily routines at a production site.
- The bottom lines. What results of the IIoT investment can the CEO and CFO see in their numbers?
Some facts about the Abdon Group
Abdon Food AB might not be as widely known as their household brands Finax and Björnekulla. Finax is as synonymous to cereal, bread, flour and oats as Björnekulla is for jam and pickles to most Swedes. Ramlösa Kvarn produce special purpose flours for the growing high-end market. With numerous mills, bakeries and production sites in the very south of Scandinavia, the annual turnover is around $100M and the number of employees is approximately 300.
The production site at Björnekulla
Björnekulla’s production facility is now, in May, surrounded by intensely yellow rapeseed fields. It is situated right in the heart of Skåne, the southernmost county of Sweden. Here, jams and pickled vegetables have been produced since 2017. The factory consists of both new and old production equipment that has been moved here from previous plants. Jams are produced year-round as the raw materials are berries that can be frozen. Pickled cucumber is more of seasonal production. The cucumbers are ripe sometime from late June to mid-July. The high season in cucumber production lasts 10-12 weeks from harvest. The equipment for cucumbers is also used in the production of pickled beets.
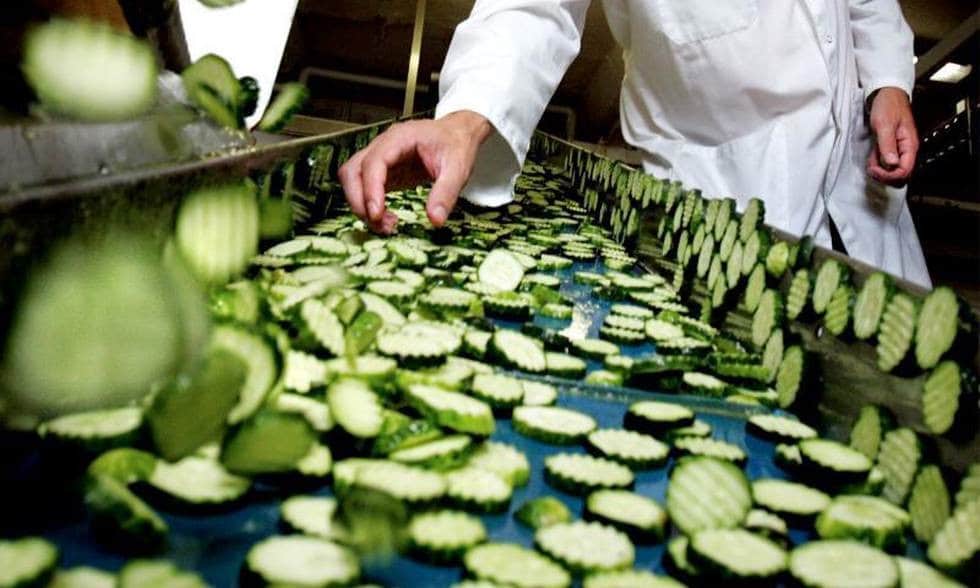
How do you want your pickled cucumbers sliced? Plain or groovy like these ones?
The production manager
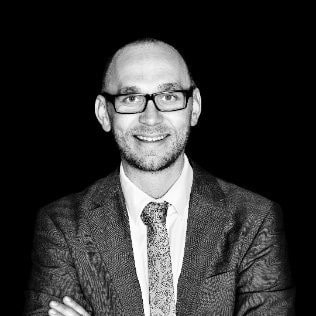
Food and numbers are Mathias Stendahl’s great passions. He has a background as both a chef and a business economist with a major as a controller. He is therefore thrilled in his role as overall production manager at Abdon Group AB, and the implementation of the IIoT platform. “During my years in the grocery trade, I was spoiled with access to a lot of statistics. For example, for FMCG, Fast Moving Consumer Goods, there is Nielsen data that shows how both your own and your competitors’ sales are going. You can see almost in real-time, the effects of campaigns, and changes in price or shelf space. It sounds like a cliché, I know, but my motto is “to measure is to know”. Here at the Abdon Group I get great support for the ideas that we need to measure more and becoming more data-driven in our production. The most notable difference with previous workplaces is probably that in production you live a little more in the present. Sometimes it is urgently needed to solve the problem and it suits me fine.”
The production line for the pilot project
“Since the production line for our jams is running continuously throughout the year, it felt natural to start the project there. Likewise, the production series are much longer than in, for example, our bakeries where in a few hours you bake several different types of bread. Jams have a long shelf life and we do not need to do all varieties every day. We have more consistent data in the jam production than anywhere else, so the effects of tweaks in the production line are more reliable.”
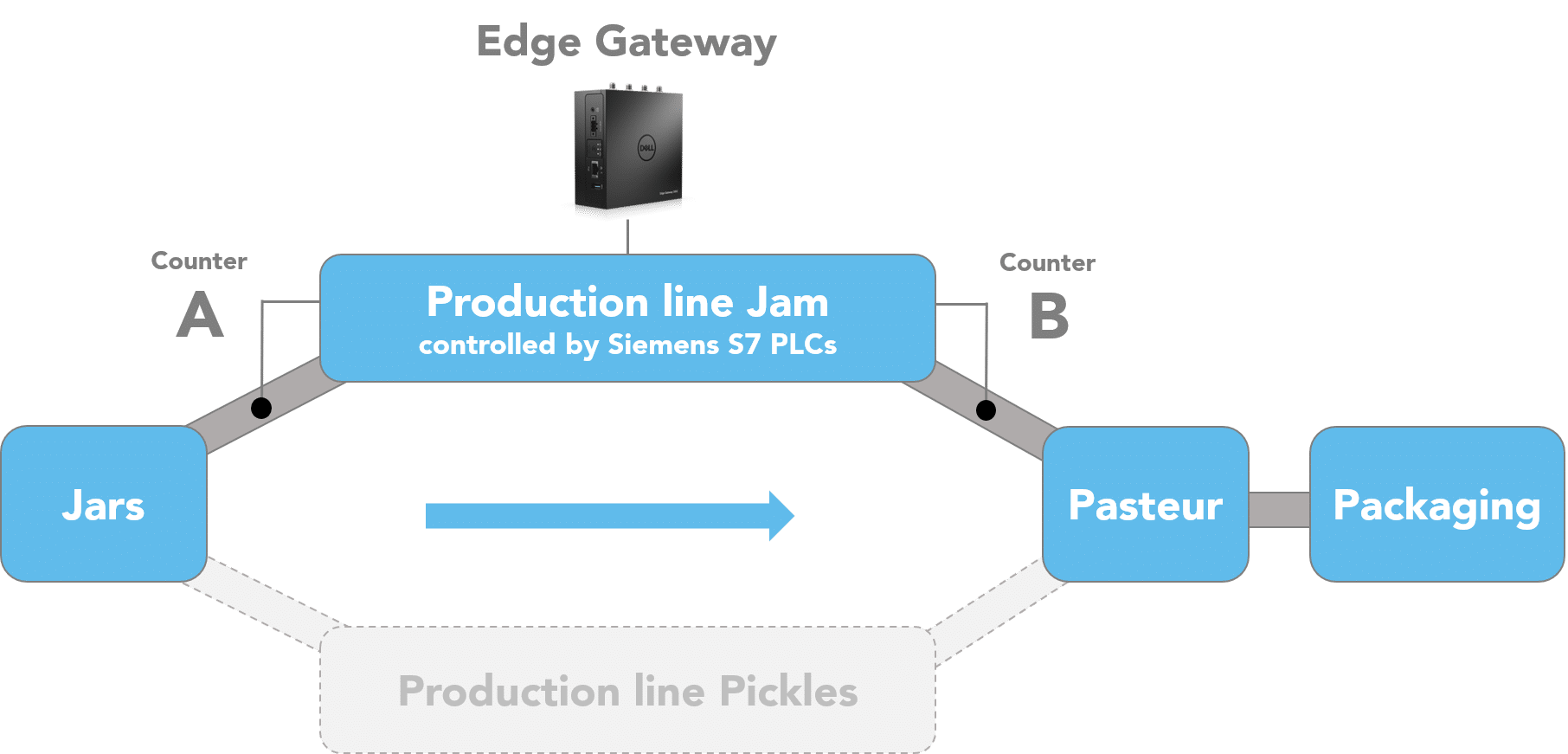
The scope for the pilot project
“In May we will launch a solution for measuring OEE, Overall Equipment Effectiveness. This means that we will know how well we have utilized our equipment and the overall quality of our processes. The line’s PLCs from Siemens provides the data for uptime and downtime, as well as the production paces during uptime. We compare these numbers to the numbers we expect from ideal conditions.
The overall quality is measured quite easily. Sensors count the number of jars entering the line at point A and the number coming out at point B. Those missing at B, after a shift, have been discarded somewhere along with the processes. OEE doesn’t care about the exact reasons for the discarding, such as wrong filling levels or a lid screwed on incorrectly. The reasons will soon be more thoroughly monitored when we deploy features for Loss Tree analysis. What we have left to do now, to complete the first step, is a little fine-tuning such as customizing the design for the public scoreboards.”
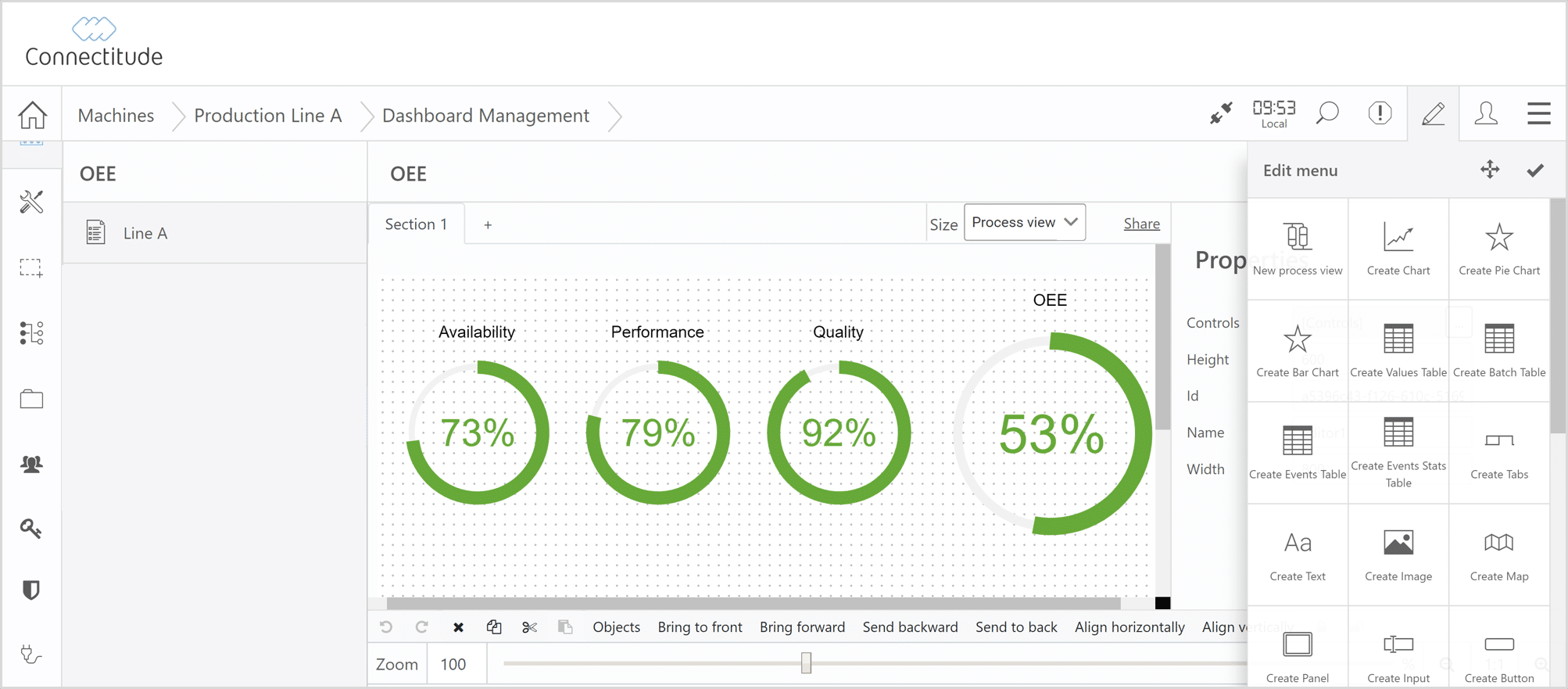
The standard user interface of the drag-and-drop design tool for creating OEE Scoreboards.
The main objective of implementing OEE
“In this first step, the main objective is to create more involvement for everyone in the production by providing fresh and relevant data. Playing soccer without keeping the scores in real-time, or not to measure the difference in how long you can jump when you try a new technique, doesn’t make much sense. It’s in our nature to crave information and to see the results of our ingenuity and our actions, even at work. OEE is an overall KPI that we believe will result in positive effects on the overall teamwork. OEE is also so universal that we, in the forthcoming step, can compare the trends for all our seven production sites. Used in moderation, rivalry is an excellent source of motivation. For the site managers and myself, it will also be a great tool to identify causes for bottlenecks in a more data-driven manner. Having all data from the shifts at hand we will know better if it’s a machine that needs to be improved or maybe the training program for the operators.”
Was it hard to connect the machines?
“Connecting the IIoT platform’s Edge Gateway directly to the PLCs was pretty straight forward. The Edge Gateway has a vast number of integrated drivers for being compatible with various industrial protocols. For this production line, the Siemens 7 Communication Protocol is used. Our regular automation consultants did all the practical work, with just some minor assistance from Connectitude.
Within the Abdon Group we had to improve the infrastructure for wireless communications at some of our production facilities. This was not only due to this project, it just speeded up inevitable progress.”
Any unexpected challenges?
”Not really. It is a great temptation when you realize how much you could measure and integrate. We needed to be hard on ourselves to start lightly and to increase gradually. It is better to focus on confirming that the first released features are stable and well received by the staff. The project has not affected our production, but the production sometimes interferes with the project. No matter how prioritized this pilot is, unforeseen events in the factory always must be resolved first. Still, we are pretty much as planned in the schedule.”
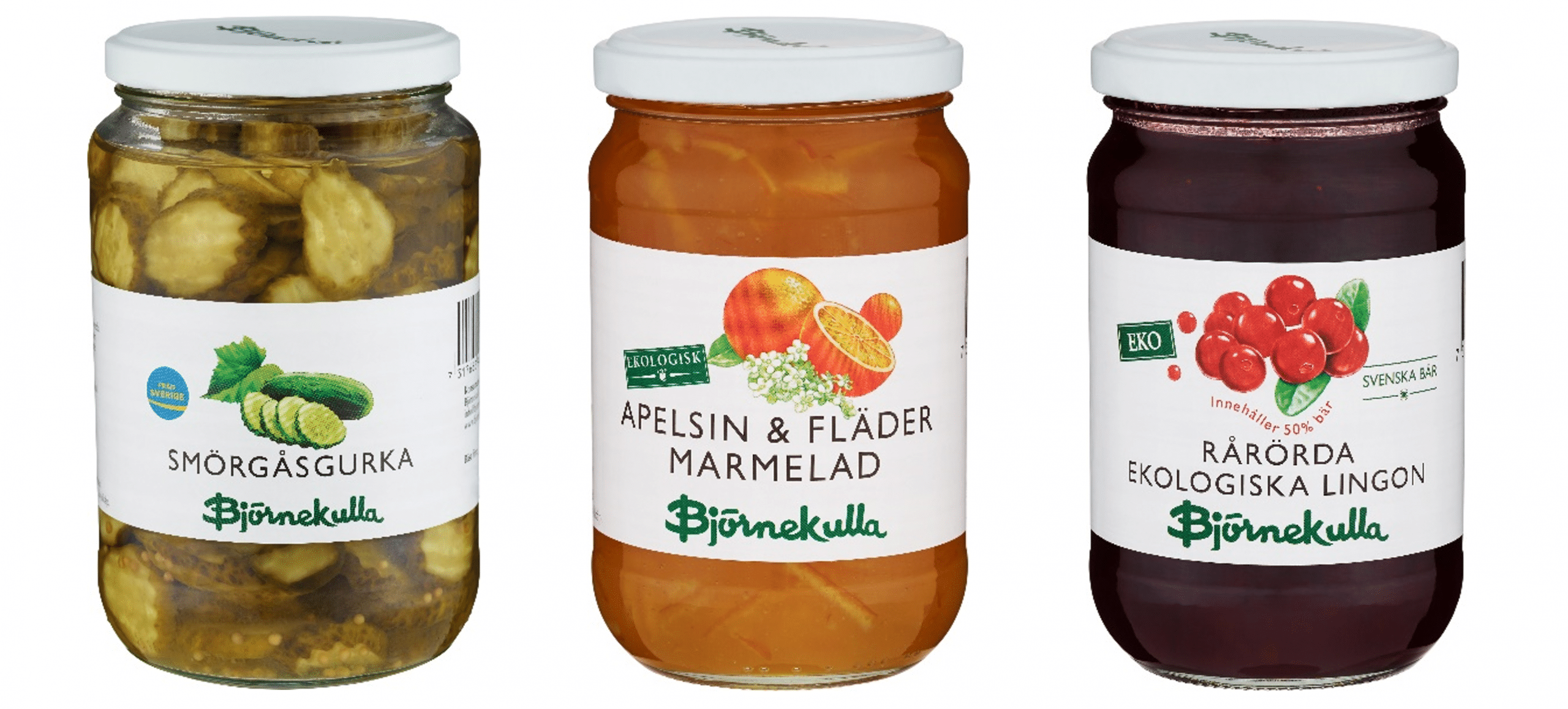
Any unexpected benefits?
“Our coolers and freezers are not a part of the production lines per se, and they are not included in our OEE calculations. However, after some trials with LoRa sensors, we realized how easy it would be to also log all their temperature data in the IIoT platform. Our work on quality assurance of our products is based on a standard for the food industry called FSSC 22000. This entails an annual audit that verifies that we have had the correct hygiene routines and handling of raw materials. It feels good to know we now have easy access to the historical data for all the important temperatures.”
What is next on your IIoT roadmap?
“After the local launch this month, we will introduce the OEE features to all our production facilities. Personally I think the Loss Tree Analysis will make a great impact on our production, so it has to be launched soon after OEE. It is more interesting for me to see what caused a stop than just stating there was a stop. Today we have a system for planning and follow up maintenance and repairs. It would be neat to integrate this system into the IIoT platform. Less administration for the staff if actual uptime and downtime for planned and unplanned actions are registered automatically by the connected equipment. The maintenance reports combined with full access to various historical data from the machines will make my investment decisions easier. I will have more information to identify when a machine needs to be replaced or just need to be used more carefully.”